S5 BONUS: Value Engineering Your Custom Home Design
The one question on everyone's mind lately is what does it cost to build a new home? For the most part, that cost is up to you! Finishes, complexity, land, and timing have a major impact on what you ultimately pay for your dream home.
However, having the right builder/architect team in place before you go into the design process is one of the most important ways you can manage the construction costs of your new home. By including your builder in the process, you can manage your costs and even mitigate some of the cost and timeline risks inherent in building a home that has never been built before.
Getting your builder and your architect involved up front is one of the key ways you can Value Engineer your new home. And if this is your first time building a custom home, you might be curious what that means and how it can help you. To discuss this approach to building, we visited Jeff Day from Jeff Day Architects in St Louis, MO to host a live discussion and take questions. And today we're sharing that conversation on our podcast so you can hear it, too!
Your Episode Tool Box:
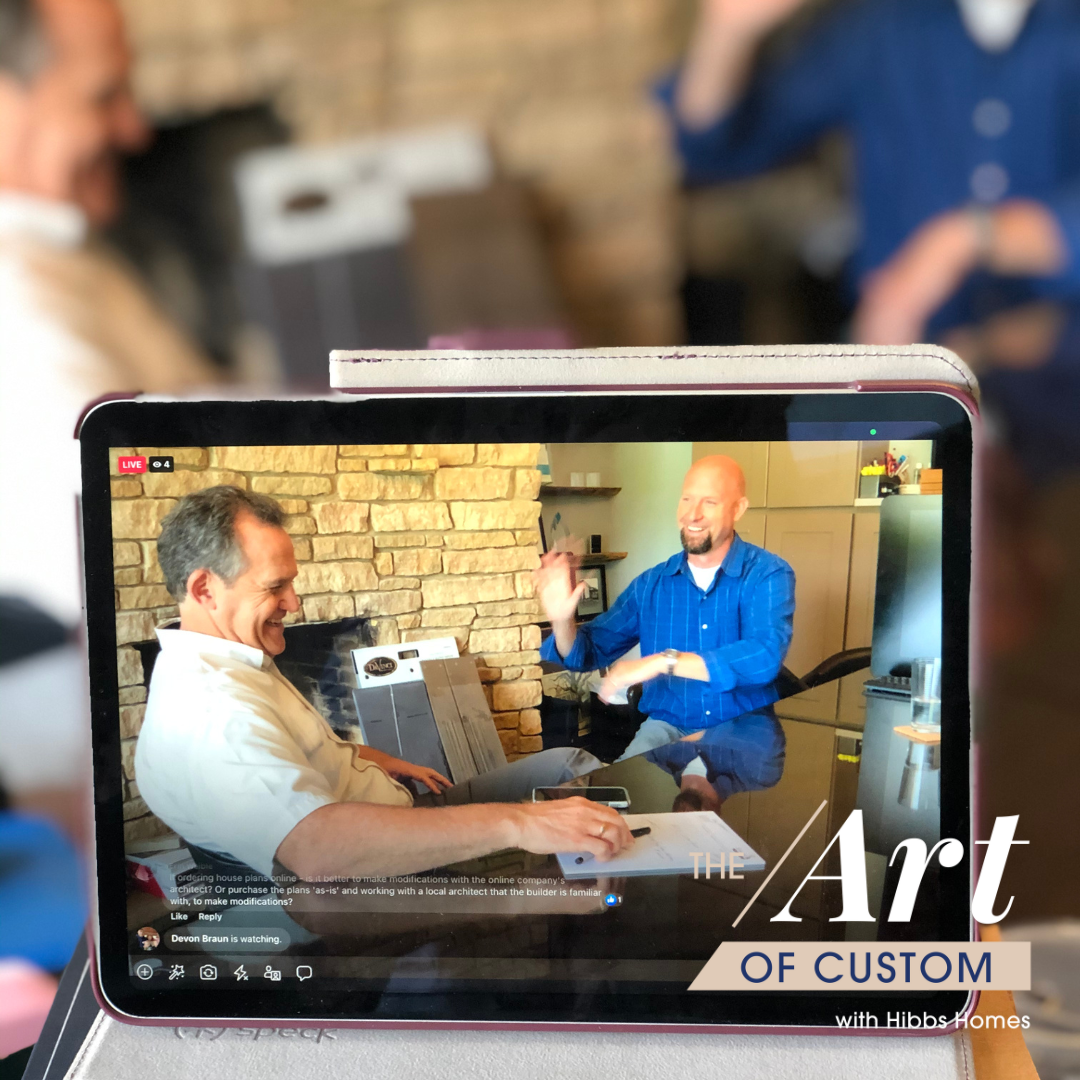
Special Thanks to Our Sponsors...
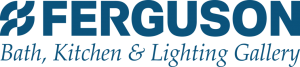
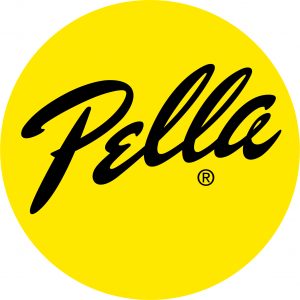
The design process is one of the most important steps in custom home construction, and can be both exciting and rewarding.
While your home's design is an expression of your unique tastes, it also has the greatest influence on your overall construction costs - including labor and material expenses that vary based on the selections and design choices you make.
If you're considering building a custom home, it's essential to have a builder on board before beginning the design process. Your builder is your advocate, and the best home builders partner with your architect to "value engineer" your home's design.
But what does "value engineering" mean? It is the key step in the process to maximize your home and construction investment.
Kim Hibbs, founder and president of Hibbs Homes, spoke with St Louis architect Jeff Day, one of our frequent building partners, to answer your questions about value engineering. They shared tips and tricks to get the most from your construction investment through the value engineering process.
This Facebook Live event was recorded July 7, 2021 at Jeff Day & Associates Architecture in St Louis, MO.
Transcript:
Kim Hibbs: Thanks, everyone, for joining us for another edition of The Art of Custom. Last time we got together, we were talking about construction financing. This time, we're going to take a different path, but it's along the same lines as that conversation. We're going to be talking about value engineering and how now really is a good time to build as long as you work hard with your architect partner, your builder partner, and really pay attention to the house's design, which we call value engineering.
And the reason I said "we" is because seated over to my left is Jeff Day. Not only a really good friend of mine, but he's also an exceptional architect here in the St. Louis area. Jeff and I have known each other for close to 15 years and done some wonderful, high-profile projects together. I don't think there's a better person to have as part of this conversation than Jeff because he understands the importance of communicating with clients and helping them understand how to value engineer their construction plans. So whether your budget is $500,000 or $5 million, you can go ahead and build.
Jeff, it's nice to have you with us.
Jeff Day: Yeah, thanks for the invite.
Kim: I have to ask you to pause for one moment because Melody Meiners is behind the camera, but you'll hear us refer to her occasionally. And she might even pop in with a question or two. So, Melody, come around to this side of the camera real quick and just say hi to everybody. That's Melody.
So, if we do refer to Melody, or if she throws us some questions, I want to put a face with the name. We welcome your questions as we go along, so feel free to ask them.
But, Jeff, when I say "value engineering" what does that mean to you as an architect?
Jeff: For me, the long and short of it is trying to get everything that a client needs and wants into a simpler package. And one would hope package then adds value by reducing cost.
Kim: So I'm going to write down the word 'simple' because I think if there's one takeaway from today, if you can simplify your design it is absolutely going to help the cost. But Jeff, I don't want to scare people away that might think 'I've got a million dollars or I've got $800,000, or whatever the budget might be, and I don't want to build a simple box.'
Can you can you build a beautiful home on a budget through value engineering?
Jeff: Absolutely. So, I think where people get lost is in all the weeds of dimensions of lumber, dimensions of building products. You know, everything works kind of in a 2-foot increment. So, a lot of these homes you'll design 41 feet 6 inches wide or something ridiculous like that, and you're not thinking through, okay, would 42 feet make more sense or 40 feet make more sense?
So that's step one of all of this, to think through wasted 2-by material, wasted sheet goods of plywood, drywall, even siding. But then beyond that, it's a matter of appendages on the house. You can build a simple box and then put a creative appendage for the garage or a creative appendage, a side porch, or front and rear porches.
And then you get to the upper level, whether there's an actual second floor where you can maybe introduce some cantilevers, again in these two foot dimensions. Or push and pull the roof structure itself. If it's just a ranch, we've done simple boxes where you take a ranch home, push and pull some of the roof trusses, and it doesn't add excessive cost. Certainly not as simple as just a basic big triangle or pyramid on the top of the house. But you can push and pull that and find creativity in it.
And then there are areas where we've done added trusses on a million plus house, if it depended on one. Those are areas where you can get a little more creative, as well, and not only reduce the primary footprint of the home and move bedrooms upstairs, but now maybe there's a little bit steeper pitch to the roof and monies saved are still in existence. You'll spend a little bit more on a steeper roof, but you're still saving money by moving things upstairs and reducing the footprint of not only the foundation but also the walls and the roof structure. So there are so many things that people just don't think about in the design process.
Kim: And that's why if you come to the table with both the builder and the architect, especially when it comes to value engineering. This not only leads to a better project but also a better experience throughout the process. Regarding added trusses, for the audience's benefit, it involves building second-floor rooms into the trusses themselves. Instead of construction exterior walls and raising them, you can manipulate the trusses and create attic trusses, which elimintaes the needs for building walls. This allows for a more economical finishing of the space around it.
Jeff: And those are built in a factory with the room inside, shipped to the site and trained in place so that the labor and everything else is greatly reduced. That's a huge deal.
Kim: It is, and there are many other tricks to the trade even when it comes to the foundation and building the second floor. As a builder, when we start thinking about budgets, we are very budget-conscious. Jeff and I always want to know where the budget is when when we work together with our various team. What is your budget? We encourage clients to be realistic with your builder and architect because we can truly plan a home around that budget and kind of work our way backward. But we need to know what the budget is up front because it helps us understand where the starting point is and then we can design the home accordingly.
Full disclosure, it's been very difficult, and we talked about this before we went live. This past year has been much more difficult primarily because of the pandemic and what it has done to the construction industry. Year-over-year, our prices are up, depending on where you live, a minimum of 20% and a maximum of 49% per year, according to a National Association of Home Builders study. Which is mind-boggling. We have been building for 18 years, and you have been designing for about that same amount of time, and we've never experienced anything like this. So we are having a much more difficult time truly understanding where these prices are going. We know they're going to back off eventually, but I guess the point is that right now is a critical time to try to truly value engineer a home. And that's what we strive for with every client work with.
Jeff: You mentioned that we want to know the price a client wants to be with at, and you know it doesn't always work out that way. The past two years have been so crazy that if you don't approach it with an ideal of not only budget and making this as simple as possible yet still attractive - I don't want to put my sign out the front yard while it's being built. And so we're pretty touchy about that. But if you can show people a more creative way to play Tetris, really - I like to use that as a reference, the old Nintendo game. You're taking these rooms and fitting them inside of this box, but you can do it in a creative way.
We had a recent project where we were given a base plan of what the client kind of wanted. Once we saw the plan and knew it was over budget, we could creatively simplify it. Now it's is a simple rectangle home, but when you walk in, the way it's all going to be laid out inside is going to be super creative. On the outside, we're going to push and pull the roof and whatnot as we're flushing out the final design. It's on my desk for review. This is going to be a really attractive craftsman-style home, and the homeowner never saw it as a simple box. But once it was all put together as a simple box, it started to take shape in his mind and made more sense. And probably cut what would you guess, 15 to 20 percent off the budget?
Kim: I think it's probably around 20 percent. The project we're talking about is located in West St. Louis County, and the homeowner had been working with an architect, but the design was too expensive to build. They needed a fresh perspective, so they came to us, and Jeff was able to quickly sketch some floor plans that were exactly what the homeowner was looking for, while also greatly simplifying the build costs. Sometimes it takes a second set of eyes to find a solution. Over the past few years, we've had several clients come to us devastated that the original plans they designed with an architect were way over budget, and we were able to help them through value engineering.
So, I tell people it's important to be persistent and not give up on your dream home design, even if you've had a bad experience. Working together as a team with your builder and architect, you can make it happen through value engineering. Too often, people get discouraged and walk away, but that doesn't have to be the end of the story.
Jeff: Yes, some of the easiest changes we've seen over the past yea have been with clients who want a new home and all the bedrooms on the main floor, a ranch-style floor plan. When you start to sprawl your foot print, it means more foundation and more roof. It's more exterior walls, which means more windows, more siding, more insulation and so on.
One example we had in Chesterfield, in West County, was with these folks who wanted a ranch home. We said we could drop the price if they'd be willing to take keep your main-floor master but move the secondary bedrooms upstairs. There's a great opportunity to save money by doing this. I don't know the exact amount for an average home, but you can absolutely save money. Like you said, come back to the table and revisit it, have the hard conversations. And the bulk of everything you want will still be there, it's just that you may move your kids upstairs.
And, I'll be honest with you, I have four kids and when they're teenagers, they don't want to be near you. They want to be able to stay up.
Kim: Absolutely. And when they're gone you can zone that area off.
Jeff: So it's your heating and cooling. But the delta between the first design and then moving the bedrooms upstairs, there was a savings of almost $40,000.
Kim: That's significant.
Jeff: It is. So you can buy nicer things, or not borrow that money, or go buy a car to put in your new garage. I mean, there are all these options.
Kim: All these options to spend that money.
Hey, since we're talking pricing and since we're talking design, especially with a lot of the homes that we are building out in Northern Utah right now, people are really looking for more contemporary designs, whether it's mountain contemporary or almost like a Frank Lloyd Wright contemporary-looking design here in St. Louis.
However, those homes do cost a little bit more to build. What are your thoughts?
Jeff: Well, there are several reasons for that. First, many contractors are familiar with residential construction. When they see an ultra-modern building, they assume it's a commercial project, leading to higher labor costs. The other side of that, though, when building contemporary homes, you often want thinner framed windows and higher-end exterior finishes. For instance, you wouldn't use the same horizontal vinyl siding found on a Colonial Home on a Contemporary home. Instead, you may consider fiber cement substitutes for real wood, like Redwood siding used heavily on the West Coast.
When moving into these sidings and lower profile windows, they must be built stringer because the frames are so thin, adding to the costs. As contemporary architecture picks up momentum in the Midwest, the volume will go up, and the costs will go down, which was seen with the Craftsman style, which was a big deal when I started my company 15 years ago.
Kim: We built many of your Craftsman-style homes.
Jeff: Absolutely, and we saw over time that products like prefabricated columns and divided light windows, whether they were three over one or four over one, started to reduce in cost as the volume of those houses increased. So I don't think contemporary homes will ever be the least expensive way to build, but I think in the Midwest we'll start seeing the costs come down just a little bit.
Kim: So, again, we're going to be on the Live a few more minutes and if you have any questions, feel free to ask us.
We did have a very interesting question. We, as builders get asked a lot - and I'm sure you as an architect would probably get asked the same question - if you're going to build a house and there are an endless number of plans online that you can look through and fall in love with, is it better to start by purchasing those plans online? Or do you need to go through an architect to have them design the home?
Jeff: Sure. So, we have a lot of clients come to us with those plans. Okay.
Kim: So they purchased the plans online $1,000 or $2,000.
Jeff: Right thinking, maybe that'll save them money and what they find is, there are cities in and around St. Louis County that don't require a licensed architect. Okay.
Kim: And that's the case with with municipalities all around the country, too.
Jeff: Yes, but there are places where you absolutely cannot get your plans approved without an architect, and there are areas where they say you only need an architect for a septic or well.
We've had clients come to us who have bought plans online, but they were designed by a company from the Northeastern United States, for example. They build differently than we do in the Midwest, and down South, they build differently again. We love our basements in Missouri, but in Texas, not so much. The dry land, expands and contracts, so they don't want basements. They use more concrete block foundations and do a slab in grade in most Southern states. so when clients come to us with plans designed for a different region, their builder may say they can't build it. Then we have to explain why, and it can be a total redraw for us.
We have also had clients who pay extra for the AutoCAD files, but the problem is they don't understand the codes and ordinances for where they want to build. We have to go through and make changes to the plans to ensure they meet local building codes and requirements.
Kim: AutoCAD is a drafting software program that you use.
Jeff: It's a science, right, to draw the plans and literally every single one of those we've had, the plans do not match the elevations of the house, and so there's a redraw. But then, it's exacerbated by the idea that sometimes they use, just one layer. You can pick an electrical layer and all the electrical parts are drawn on that. You can draw a structural layer with only structural, you turn these off and on. Well, we've gotten sets of plans where all of that is on one layer, so you can turn anything off. So now we have to spend the time to not only put everything on the right layer, but then probably correct and coordinate. So there are a lot of challenges that come with it.
I think the most important challenge, though, is that if it's not drawn the way you would build it in St. Louis, you're not going to get a solid price from a builder. He's going to guess on everything, and then you just have to deal with the aftermath of that, you know.
Kim: Yes, you also mentioned Structural Engineering because that's a very important component that changes all across the country depending upon snow load, wind, earthquake, and all sorts of things.
So, I think to Jeff's point, what we found to be the most successful way of building a floor plan is not purchasing the plans, but using the plans that you see online as inspiration. Print them off, bring them to your builder, bring them to the architect, and say, "This is what we want to build. We want to start with this floor plan. We want to tweak it this way. We like this elevation." That will save you time because the way most Architects work is at an hourly rate up front during the design phase, right?
So if you save them time by saying, 'This is the house we want to build,' that's where you're going to save your money. In the long run, you'll end up spending more to manipulate the plans that you you purchased online to meet the local codes. Whether you're building here, Utah, California, Washington - it doesn't matter. Everybody has local codes that have to be met. That's why the plans online are more difficult to make work. I'm not saying you can't do it, but it's been our experience that it's more difficult to make that work, right?
Jeff: Yeah, and the other reality that needs to be understood is that those are copyrighted, right? So when you come to your builder or architect with ideas, you can't use them verbatim. We'd love to have a conversation about how you think you're going to live in the house and how our other clients are living in their homes so that you can get a a full understanding of what's possible with your home.
You really want to look at it for room adjacencies and other details. Sometimes you'll find a house online with a west-facing dining room. That's not a good idea because you don't want to eat dinner when the sun's blasting through the windows. So you want to have that full conversation about how you're going to live in your home. It may very well make the new plan dissimilar to the one you brought in, right? But it's absolutely great for talking purposes
Kim: That was really a great question. We thank you very much for that. It will be here, just a couple more minutes if any other questions come up.
Since we're talking about pricing, the last time we were, we did our Art of Custom Live, we talked with Trisha McConkey who is one of our lenders from the St. Louis area. We were discussing why now is a good time to build despite the fact that every time you turn on the nightly news, you hear about lumber prices spiking and construction costs going up, causing the and the cost to build a new home to increase between 20 and 49 percent.
I want to circle back around because we've had a few changes. For example, you and I were talking just a few minutes ago about how lumber futures, meaning lumber that will be purchased in the future, have decreased significantly.
Lumber is measured in 1,000 feet. Technically, what they do is they measure a thousand lineal feet of lumber and then establish a value for that lumber. Before the pandemic, it was somewhere in the price range of $300-$400 per thousand feet at its peak. Just a couple of months ago, it was at $1,700 per thousand board feet, which is just mind-boggling.
Recently, lumber futures have come out showing the futures down in the $900 range. As you can see, there has been a pretty big step back in lumber prices. We hope that someday that will settle closer to that $400 to $700 range, but we don't know for sure.
Copper is another material really shot up quickly, but we are now seeing that price come down due to a supply and demand issue that has started to ease off. Our electricians are saying that the cost of running of your electrical wires is going to come down a little bit. However, most other trades, like roofing, concrete, steel, drywall, and other construction-specific materials have all gone up in price and it is becoming the new norm. So, we don't really expect to see many pricing decreases with other materials.
So, from our conversation earlier, if lumber prices are backing off and some of these other prices are going to stay where they are, that could prompt somebody say, "Okay, with low interest rates, now's a good time to build." And you agree with that?
Jeff: I as we start to ease out of unemployment and people start returning to work, production will increase, allowing for larger volumes to be handled and ultimately resulting in some price reductions. However, you have to consider not only the decreasing cost of goods but also the increasing interest rates and find the right balance to strike. I also think if you delay your construction while others don't, your builder may not have time for you.
Kim: Yeah, valid point.
Jeff: You have to consider if waiting for prices to come down is worth it, especially if interest rates are going up and other people are still starting projects. In this case, Hibbs pipeline is getting crowded with projects. You might say you're willing to wait 18 months to start, but who knows what it looks like in 18 months. At that point, who knows what prices and interest rates will look like.
Kim: According to the National Association of Home Builders, interest rates are going to ease their way up over the next year to year and a half with the largest uptick potentially occurring in 2023. In my personal opinion, this presents a window of opportunity for those considering planning a home. Allowing three to four months design time, plus a month for your builder to acquire permits. Building a home requires find land to build on and other considerations.
We typically advise clients to allow four to six months up front after you've found a lot, complete the design and permitting process, then allow a month or two for budgeting and financing before you are ready to begin construction. Depending upon the size of the home, the actual construction can take anywhere from from eight to twelve months. Given the current market conditions where construction costs may ease while interest rates are low, it is an excellent time to contact a builder in your area.
When people ask me for recommendations on finding builders and architects, I suggest starting with your local Home Builders Association. The websites for the associations have drop-down menus of members who are committed to the industry, continuing education, are active in and give back to their community. It is an excellent way to find a builder. What's great way to find an architect?
Jeff: Well, let me add to that, Just as important, there are also builders from the Home Builders Association who are committed to pushing the pricing down. They're fighting tariffs and more, which helps all the consumers.
As for the best way to find an architect, most of our work comes word of mouth, which is certainly a great way to find a builder too. But I think with with Google, you can actually make a list of the things you want in an architect, such as sustainable design, craftsman-style, modern, etc. and search those things in your area to see comes up. Don't don't just go for the one that shows up at the top because they're paying for an, right? Do your homework and find the right architect for you.
Kim: Another real question came along, and it's right up our alley. The question is about whether you should consider building a SIPs home versus a traditionally built stick home. We built the Active House project in Webster Groves, and it was exclusively a SIPs home.
SIPs costs more, there's no doubt about it, but there are some benefits. As a high-performance, green, sustainable architect, give me your take on it.
Jeff: Candidly, I think the biggest benefit is how quickly they go together. You're given a paint-by-number roadmap and you drop these panels in place and bolt them all together, which it saves quite a bit of time. They're also prepared in a factory, which means they're going to be a lot more durable and straight right than traditional stick-built homes.
Kim: Let me just say that building with SIPs requires extremely careful planning as everything from plumbing chases to window openings must be accounted for in advance. If something is missed, it can be difficult to correct once you're in the field.
Jeff: In the Dogtown neighborhood in St. Louis City, we built a SIPs home right next to a traditionally framed home. And while errors can occur during the construction process, it was much easier to correct issues in the traditionally framed home than in the SIPs home. Although the two homes were exactly mirrored, correcting errors in the traditionally framed home was much easier. So, you're absolutely right, you have to be very precise with everything when building a SIPs home.
Kim: By the way, SIPs stands for Structural Insulated Panels. Essentially, you have two layers of sheathing on the outside and a thick core of foam on the inside. And inside the home it is a stud wall.
So, where do you come down on this whole pricing issue? Yes, it goes together more quickly so you're saving financing costs, but it's been our experience that while SIPs perform exceptionally well from the standpoint of efficiency, acoustics, everything that goes along with them they do cost more. Is it worth an extra cost?
Jeff: Not in my opinion. Okay, I think that flash and bat...
Kim: By the way flash and bat is using a combination of foam and traditional insulation on a house.
Jeff: You and I have built almost every building envelope type except hay bale, which is not very popular in St. Louis. Maybe a little too granola for the Midwest. However, we have found that the flash and bat actually performs at just a fraction less than the SIPs. The other reality is, with the SIPs, you'll need to come back out and seal everything, anyway, so there is still an insulation subcontractor involved in some capacity. So, for my money, I think flash and bat would probably be the best way to go unless you need to be under roof quickly because of weather or other reasons.
Kim: I agree with your assessment on that.You could also have your your wall panelized and brought out, like framing in the field, only it is done in the factory as well. So, I agree with you a hundred percent. We've built with SIPs, but I like your assessment on an upgraded installation package. These are great questions, but the way.
And if you're looking for builders, designers, and architects who understand high performance and green construction, it is essential to interview them. Building a high-performance home is a science, and it matters how these homes come together.
Just installing high-efficiency lights or cost saving appliances doesn't make someone a green builder. It's crucial understand that. I know, Melody's giving us the wrap-up signal, but before we go, I have to mention something. Chris Pedigo is our director of construction, and he reminded me that Jeff Day is truly a full-service architect. We have a client building in Lake St. Louis and there is a fantastic story about it.
Jeff: Well, I have a lot of friends, but during a site meeting with Chris, and the client, and me, we decided to find some air conditioning and start sketching out the road map for the house. On our way to a restaurant on the lake, we texted my buddy that lives there, and he came and picked us up. Mike Miller, shout out to Mike, picked us up on his pontoon boat and took us out on the late to show the client their lot from the lakeside, which they had not seen yet. It was kind of a fun experience.
Kim: That is a full-service, architect! Thank you guys very much, it's been a pleasure. By the way, I need to to let everybody know that if you if you're looking for ways to simplify your house, on our website, hibbshomesusa.com, we have a document called "9 Ways to Simplify Your Home Design and Save." Look that up.
Jeff Day your website address is Jeffdayllc.com. So it's jeffdayllc.com
Melody - thank you, for coordinating this. Thank you everyone for for joining us and we look for another scheduled Art of Custom Live coming up next month. We hope you'll join us then.